Understanding the Synthesis of Metal-Organic Frameworks
Understanding the Synthesis of Metal-Organic Frameworks
Metal-organic frameworks are large-surface-area materials structured for extreme porosity. They are typically polymers containing metal clusters or ions connected to organic ligands that form a 1D, 2D, or 3D structure. The method of MOF synthesis determines these structural properties and other key characteristics. Thus, altering certain conditions (solvent type, modulator inclusion, synthesis temperature, synthesis time, etc.) enables manufacturers to fine-tune the essential properties of metal-organic frameworks. They can subsequently be produced with distinct topologies, ones that may not have been achievable without mechanochemical or ionothermal techniques, and enhanced attributes, including stability and crystallinity. Read on to learn more detail about the process for synthesizing metal-organic frameworks.
Selection of Metal Ions and Organic Linkers
The foundation of metal-organic framework synthesis lies in the judicious choice of metal ions or clusters, also known as inorganic nodes, and organic linkers. Commonly used metal ions include transition metals like zinc, copper, and iron or zirconium and aluminum. These metals offer diverse coordination environments and oxidation states, influencing the resulting framework’s stability and functionality. Organic linkers typically consist of polycarboxylates, imidazolates, and pyridines, which possess multiple binding sites to facilitate the formation of robust coordination networks.
The combination of specific metal ions and organic linkers determines the metal-organic framework’s:
- Structural topology
- Pore size
- Chemical properties.
For instance, carboxylate-based linkers can form strong coordination bonds with metal ions, resulting in highly stable frameworks. Conversely, imidazolate linkers, known for their rigid structures, contribute to the formation of zeolitic imidazolate frameworks (ZIFs), which exhibit high thermal and chemical stability.
Solvothermal Synthesis
Solvothermal synthesis is the predominant method for metal-organic framework fabrication. It involves the dissolution of metal salts and organic linkers in a suitable solvent. This mixture often includes a modulator, such as an acid or base, to control the pH. It also influences the growth of the crystalline structure. The reaction solution is then sealed in an autoclave and heated to elevated temperatures. These temperatures typically range from 80°C to 220°C, under autogenous pressure.
During this heating process, the reactants undergo nucleation and growth, leading to the formation of metal-organic framework crystals. Choices of solvent, temperature, pressure, and reaction time are parameters that affect the resulting metal-organic framework’s:
- Crystallinity
- Morphology
- Size.
For example, higher temperatures generally promote faster nucleation rates and larger crystal sizes. However lower temperatures can yield smaller, more uniform crystals.
Self-Assembly and Crystallization
Under solvothermal conditions, the metal ions and organic linkers self-assemble through coordination bonds. This can result in the formation of crystalline metal-organic framework structures. The self-assembly process is driven by the coordination preferences of the metal ions and the geometric constraints imposed by the organic linkers. Its coordinated interaction leads to the spontaneous formation of ordered, porous networks.
The crystallization process is highly dependent on the precise control of reaction conditions. Slow crystallization can result in well-defined, high-quality crystals. Rapid crystallization might produce amorphous or poorly defined structures. Researchers often employ techniques to steer the crystallization process towards the desired framework architecture, such as:
- Varying solvent polarity
- Using mixed-linker systems
- Introducing templating agents.
Purification and Activation
Once the metal-organic framework crystals are synthesized, they undergo purification to remove unreacted precursors and solvents. This typically involves washing the crystals with fresh solvent. It can also apply solvent exchange processes to replace the mother liquor with a more volatile solvent. The final step in MOF synthesis is activation. It entails removing guest molecules from the pores to generate the desired porosity and surface area.
Activation is usually achieved through thermal treatment under vacuum or flowing gas to desorb the solvent molecules trapped within the pores. The choice of activation method can significantly impact the final properties of the MOF. For example, mild activation conditions are necessary for thermally sensitive metal-organic frameworks. However more robust frameworks can be used to withstand harsher activation protocols.
Factors Influencing Metal-Organic Framework Synthesis
The synthesis of MOF materials is a delicate balance of various factors, including:
- Temperature
- Pressure
- pH
- Solvent choice
- Reaction time.
Each parameter must be meticulously optimized to achieve high crystallinity, purity, and porosity. Furthermore, selecting metal ions and organic linkers can tailor the metal-organic framework’s properties for specific applications. Advanced techniques, like in situ monitoring and computational modeling, are increasingly employed to control the synthesis process. This can enable the rational design of metal-organic frameworks with targeted functionalities.
Utilizing Synthesis to Unleash the Potential of Metal-Organic Frameworks
The strength of metal-organic frameworks lies in their ability to be easily adapted through synthesis. Whether they are applied as nanoporous materials, combined with metal hydrides to enhance their ability to store hydrogen, or used in an application like catalysis or drug delivery, utilizing a specific method of synthesis can improve certain attributes and make them well-suited to a specific application. Their porosity, large surface areas, that can total around 7000 m2/g, and modifiability also makes them extremely useful in areas that require materials for gas separation or storage. Understanding these characteristics requires the application of specific equipment. We, Hiden Isochema, have instruments available to support this analysis, such as our IGA-001 gravimetric analyzer. Discover additional information about our equipment for metal-organic frameworks by visiting our nanoporous materials page now.
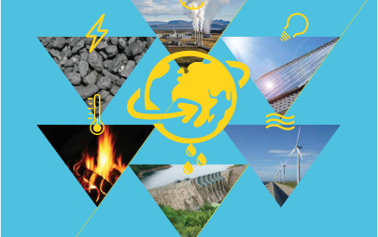
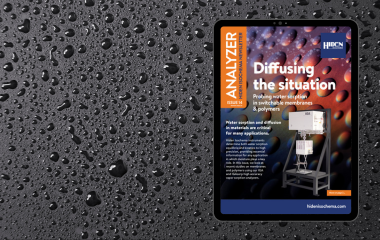